用途と実績
OHRミキサー
浮上分離 マイクロ・ナノバブル 乳化 均一混合/均一微分散 オゾン処理 中和処理・pH調整 その他の実績例
OHRエアレーター
散気管 堆積物巻上げ 脱気 気−液反応
従来技術の限界 |
OHR技術 |
圧力タンクを使うため、日々の圧力調整に苦しむ。
また圧力タンクは、定期更新が必須。 |
圧力タンクはまったく使わない。
運転調整は最初の1回だけで、あとは一切不要。 |
高圧ポンプ・高圧エアーが必要。 |
注入エアー圧は、ごく低圧の0.1MPaほど。
使用ポンプは、通常の水ポンプと同等の定格電力で済む。 |
マイクロバブルの出来が悪く、SSの分離性能が悪いため、多量の凝集剤に頼らざるを得ない。 |
良質なマイクロバブルを非常に安定して生成できる。
凝集剤は2~3割減が普通で、最大で5割減の実績あり。 |
大量の排水処理に対応するには
複数台を設置するなど、巨大・複雑な装置となる。 |
OHRミキサー1本+ポンプ1台で、最大15,000ℓ/minのマイクロバブル水を生成。
最小限のポンプ動力と配管構成で済む。 |
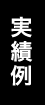 |
- 毎分1,800ℓの大量マイクロバブル水を、OHRミキサーMX-F80型+22kWポンプで生成。

- 油脂含有排水のSS、n-Hexを無薬注(凝集剤無添加)で浮上分離。
- 既設の浮上分離装置にOHRミキサー単品を取付けて、分離性能を著しく改善した実績多数。

|
従来技術の限界 |
OHR技術 |
ごく少量しか作れない技術がほとんどで、ラボ試験用や小規模装置向けにしか使えない。 |
毎分10ℓから、毎分15,000ℓまで対応できるため、巨大な排水処理設備や化学反応設備にも対応できる。 |
マイクロ・ナノバブル化できる気体が限られていたり、純水では作れない技術がある。 |
気体・液体の種類は問わない。 |
装置が複雑で、圧力タンクや高圧ポンプを使う。
溜めた水の中でしか生成できない技術もある。 |
OHRミキサーとポンプさえあれば、インラインで安定的にマイクロ・ナノバブルを生成できる。 |
マイクロバブルだけ、あるいはナノバブルだけ、と生成できるバブルが限定的な装置がほとんど。 |
簡単なバルブ操作だけで、マイクロバブル / ナノバブル/ 粗大バブルの3種を、用途に合わせて作り分けできる。 |
圧力差を利用してマイクロ・ナノバブルを生成するだけであり、微細気泡と対象液の接触・反応は自然任せ。 |
OHRミキサー内部で、マイクロ・ナノバブル生成と気−液の接触・反応が同時に行われる。
つまり1本のパイプが、反応設備の代わりとなる。 |
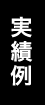 |
- 窒素置換法による脱酸素(窒素マイクロ・ナノバブル生成)。

- 有機溶剤+CO2ガスの反応。反応時間は11時間 ➤
6~7時間に、CO2ガス量はほぼ1/2に。
- 5,000m3/日もの着色排水を、廃オゾン処理設備なしでオゾン処理。

- 微細気泡孔リッチの、ウレタンスポンジの製造。
|
従来技術の限界 |
OHR技術 |
乳化剤(化学薬品)を添加せずに乳化させるためには、非常な高圧が必要。 |
軽油+水の場合、わずか0.3MPaのポンプ圧力で、乳化剤を添加せずに、ワンスルーで乳化できる。 |
巨大・複雑・高額な乳化装置が必要。 |
OHRミキサー+ポンプだけで、高圧乳化機の代わりとなる。 |
定期的なメンテナンス・部品交換が必要で、メンテナンス体制が整った環境でないと使えない。 |
OHRミキサーは、可動部・交換部品・消耗部品なしで、完全メンテナンスフリー。 |
処理量が限られているため、大量に乳化液を作るには、たくさんの乳化機を揃えなくてはならない。 |
OHRミキサー1本+ポンプ1台で、最大15,000ℓ/minの処理量まで対応できる。 |
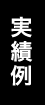 |
- 2,000万円もの高圧乳化機を、わずか38万円のOHRミキサーに交換し、製造設備で使用中。
使用圧力は、従来設備の1/100ほどで済んだ。
- スピーディーに、かつ大量の豚骨スープ(乳化液)を作るために使われている。
- その他、270件以上の納入実績あり。
|
従来技術の限界 |
OHR技術 |
大きなタンク内で、撹拌羽根で撹拌しながら均一分散するまでかき回し続ける。 |
ワンパスの瞬間処理。
A流体とB流体を、OHRミキサーに通すだけ。 |
巨大・複雑・高額な装置で、時間をかけて混ぜる。 |
OHRミキサー+ポンプだけで、ワンスルーで均一混合が完了。 |
定期的な分解洗浄の際には、構成部品が多いため時間と手間がかかる。 |
OHRミキサーは、自分で自分を洗う作用があるため、洗浄液を通して運転すれば済むケースがほとんど。 |
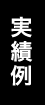 |
- 食用油に、極微量(3.0ppm)の添加物を混ぜるために使用。
ワンパスで完全均一分散できることが確認できたため採用。全グループ工場で使われている。
- A有機溶剤中に極微量の水を混合する目的に使用。どのような混合機を使っても混ぜることが出来なかったが、OHRミキサーを使ったところ初めて均一混合が達成できたため導入。
- 高粘度液に、油性香料を均一微分散。
- ビタミンCの粉体を、食用油中に均一微分散。

|
従来技術の限界 |
OHR技術 |
巨大な槽に排水を導き、オゾンガスをバブリングして、時間をかけて接触・反応させる。 |
OHRミキサー内で全ての排水と、全てのオゾンガスをインラインで接触・反応させる。 |
多量の未反応オゾンガスが放出されるため、それを分解する設備が別途必要。 |
未反応オゾンガスがほとんど出ないため、廃オゾンガス処理設備なしでもオゾン処理が可能。 |
巨大な反応槽、大型のオゾナイザー、廃オゾン処理設備が必要なため、設備費が非常に高額。 |
従来方式に比べ、設備全体を大幅にコンパクト化できるため、ある現場では従来方式の1/3の価格で導入できた。 |
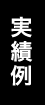 |
- 5,000m3/日もの大量排水を、廃オゾン処理設備なしでオゾン処理できた。

- オゾン単独では分解できないとされているダイオキシンが分解できた。

- 電炉製鉄所における、3,000Nm3/minもの猛烈な悪臭排ガスを、高濃度オゾン水噴霧によって完全脱臭できた。
|
従来技術の限界 |
OHR技術 |
大きなタンク内で、撹拌羽根を使って任意のpHになるように調整するが、不均一な混合しかできないため、ハンチング(酸とアルカリの往復現象)に悩まされる。 |
OHRミキサー内で処理対象液と薬剤を完全均一混合し、反応させるため、ハンチングが最小限で済む。 |
薬剤が不均一に混合している状態でpHを測定し、薬剤を追加注入するため、いつまで経っても任意のpHにならず、薬剤を無駄に消費する。 |
注入した薬剤は、OHRミキサーを通過する一瞬のうちに均一に混合されるため、無駄に薬剤を使う必要がない。 |
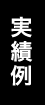 |
- pH0~1という強酸廃液を苛性ソーダによって中和処理する工程において、従来方式ではハンチングが頻発し困っていたが、OHRミキサーを使ったところハンチングなしで中和処理ができた。
薬剤の無駄がなくなったため、苛性ソーダの使用量を30%も削減できた。
|
OHRミキサーの、その他の実績例 |
|
- 顔料を酸化させながら、有機溶剤中に微分散させる。

- 乳化を破壊するために、乳化液に高剪断力を与える。
- ジェット機燃料中の含有水分が、航空機の飛行中に凍結することを防ぐために循環ミキシングする。
- メタンハイドレートを人工的に製造する。
- 薬品を一瞬で、精確な濃度に希釈する。
|
従来技術の限界 |
OHR技術 |
必ず目詰りするため、定期清掃・交換を強いられる |
原理的に目詰り無し。15年経っても、新品時の性能をキープ。
 |
槽から水抜きしなければ、設置・交換できない |
槽からの水抜き無しで、設置できる。
 |
高い効率をPRしているが、実際の排水では、著しく効率が低下する |
実際の排水でも、清水時と同等の効率を発揮する。
(アルファ値=ほぼ1.0) |
エアーの上昇速度が遅いため、槽内を均一撹拌できず、槽底に還元質の嫌気ゾーンが生じる。 |
エアーの上昇スピードが非常に速く、槽内に強力な循環流を形成するため、槽底に汚泥が堆積しない。 |
流体をミキシングする作用はないため、【化学反応設備の改善】テーマには使われない。 |
猛烈なミキシング作用があるため、【化学反応設備の改善】テーマで、積極的に使われる。 |
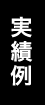 |
- 納入実績3,400事業所超。そのうちの9割以上が、水抜きなし・アンカー止めなしで設置。
- 某化学工場では、汚泥貯留槽の撹拌のために、26年間ノーメンテで使用。

- SS:30,000mg/ℓの排水で、12時間おきの間欠運転をしても、18年間目詰りなし。

|
従来技術の限界 |
OHR技術 |
重質物質を巻き上げる力が弱く、どうしても槽底に堆積してしまう。 |
OHRエアレーターに独特な、猛烈な「らせん流」によって、散気管内部に強力な負圧が形成されるため、重質物質であっても猛烈に巻き上げる。 |
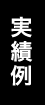 |
- 石灰30%スラリーでも、槽底に堆積を生むこと無く、19年間目詰りなし。

- 1年に1回、最大1.8mもの炭酸カルシウムの堆積を清掃していたが、OHRエアレーター設置後は堆積が視認できないほどの顕著な改善ができた。

- フェントン反応において、反応促進のための撹拌・混合と、析出物の堆積防止を目的として使用。
|
従来技術の限界 |
OHR技術 |
動力式の水中曝気装置や、多孔質の散気管でバブリングするが、低効率のために過剰なエアーが必要であったり、しつこく残存する物質が除去しきれなかったりする。 |
OHRエアレーターは、液体と気体の両方を砕き、液中の残存物質をたたき出す作用があるため、一見すると強力そうな動力式の装置よりも高効率を示す。(※OHRミキサーを使ったインライン処理も選択できます。) |
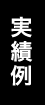 |
- 動力式の水中ジェット機ではまったく脱気できなかったVOCが、OHRエアレーターでは除去できた。
- 2~3万ppmもの大量消石灰とVOCとを含む排水からVOCを脱気させるために、OHRエアレーターを使用。従来は散気管の目詰りに困っていたが、定期洗浄は完全にゼロになり、吹込みエアー量は40%削減できた。
- 廃酸中の亜硫酸ガスをエアー曝気によって脱気処理。
|
従来技術の限界 |
OHR技術 |
よく行われる気−液反応の方法は、気泡塔(縦型タンク)の底部で気体をバブリングするやり方であるが、大きなバブルを単に吐き出すだけでは、その大部分が液体と接触せずにタンク外部へ放出されるため、非常に効率が悪い。 |
OHRエアレーターは、内部で気−液を激しくミキシングする構造であるため、単なるバブリングとは比較にならない高効率を示す。(※OHRミキサーを使ったインライン処理も選択できます。) |
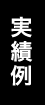 |
- SO3をSO4に酸化処理するためにOHRエアレーターを採用。従来使用の散気管に比べて2倍の効率であった。
- 消石灰含有廃液にCO2含有排ガスを吹込み、炭酸カルシウムを生成する。
- 用水中の鉄分をエアー酸化によって分離除去する。
|