Home › OHR AERATOR — real-world examples
OHR AERATOR — real-world examples
Instantaneous gas–liquid reaction diffuser
Sludge accumulation prevention and removal
Calcium carbonate accumulation drastically reduced
- Wastewater volume: 24,000m3/day.
Calcium carbonate (CaCO3 with a specific gravity of 2.7) accumulated in large amounts (average 0.9 m, maximum 1.8 m), and removal of this accumulation took two weeks every year.
- After switching to OHR AERATORs, accumulation fell drastically and running conditions improved to the point that no accumulation was observed even when the water was drained from the tank.
- Installed OHR AERATORs: model AE-130N × 424 units
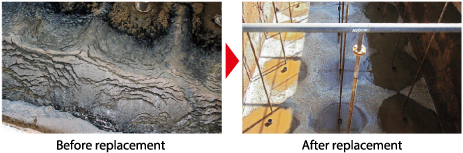
No clogging for 20 years, even in a tank with 30% lime slurry
- The MLSS is 15,000 mg/L, of which 30% is lime. The water depth of 7.0 m is significantly deeper than the average water depth for an aeration tank (4 to 5 m).
- The conventional air diffusers in use before the OHR AERATORs were introduced had to be jet-washed once a month to unclog them.
- There has been no clogging in the OHR AERATORs for 20 years (since February 1998).
- Installed OHR AERATORs: model AE-130 × 56 units × 2 tanks = 112 units total
Maintenance-free operation and power saving
Maintenance-free for over 26 years
- Chemical plant
- Used to churn excess sludge in a holding tank (SS: 20,000 mg/L)
- This photograph was taken at the time of inspection. The OHR AERATORs showed no signs of frictional wear or changes in shape; they remain as good as new and can be used for a long time to come.
No clogging for 18 years despite harsh intermittent aeration
- Sugar processing plant
- Wastewater contains high levels of calcium and magnesium (SS: 30,000 mg/L).
- Absolutely no clogging for 18 years despite intermittent aeration (12 hours on, 12 hours off) every day. Not a single washing has been performed.
(Photograph taken at time of inspection)
Maintenance-free for 20 years
- Brewery
- Installed OHR AERATORs: model AE-130 × 320 units
- OHR AERATORs were introduced in order to eliminate clogging and save energy.
Maintenance-free for 15 years
- Chemical plant
- Installed OHR AERATORs: model AE-130 × 20 units
- The plant had been using conventional porous air diffusers, but low OTR prompted the switch to OHR AERATORs, which have provided exceptional maintenance-free performance ever since.
Maintenance-free for 16 years
- Dairy plant
- Porous air diffusers frequently clogged due to being used in an SBR (sequencing batch reactor).
This is a method in which aeration, sedimentation and effluent discharge are performed sequentially in a single tank. The need to stop aeration during the latter two processes frequently causes clogging in conventional air diffusers.
- Prior to introducing OHR AERATORs, the DO at the floor of the tank was zero, and sludge bulking was an issue. The SV30 value was 95, meaning virtually nothing had sedimented.
- The newly-installed OHR AERATORs managed to maintain a tank floor DO of around 3.0 mg/L as well as eliminate filamentous bacteria, thereby eradicating the bulking issue and greatly improving the SV30 value to 30–50.
The OHR AERATORs also made it possible to cut the number of aeration tanks from four down to two, reduced electricity costs by almost 27%, and simplified operations to the point that the two full-time staff could be replaced by one person working half a day.
Maintenance-free for 16 years
- Dyeworks
- This factory had been using porous air diffusers, but they required annual cleaning.
- OHR AERATORs were introduced to eliminate clogging and reduce energy usage. This made it possible to stop one of the two air blowers, and by operating the remaining one at 40 Hz with the use of an inverter, electricity costs fell by some 70% in total.
Maintenance-free for 21 years
- Food production facility
- Installed OHR AERATORs: 6 units per tank × 6 tanks = 36 units total, installed against the tank wall in a single spiral roll arrangement.
- Following many years of success in the aeration tanks, 30 model AE-130Ns were installed into the raw water tanks in April 2015.
Maintenance-free for 13 years
- Brewery
- MLSS: 8,000 mg/L
- This facility had previously used porous air diffusers for bubbling, but switched to simple perforated pipes because of issues with clogging. However, DO only increased to around 0.3 mg/L, even on non-business days with no sewage inflow.
- OHR AERATORs were introduced to increase DO and remove the need for maintenance. After just 15 hours of aeration, the DO rapidly increased up to 0.8–1.9 mg/L.
OHR AERATORs were subsequently installed in the equalization tank, where they completely eliminated the foul odors.
Maintenance-free for 17 years
- Vegetable juice factory (new facility)
- Installed OHR AERATORs: model AE-130N × 40 units (including in the raw water, equalization and neutralization tanks)
- This facility installed a Decompo, equipment from OHR that reduces sludge volume. In this extremely rare case, this proved sufficient to decompose the entirety of the excess activated sludge, meaning none had to be sent away for disposal. No dehydrator has ever been installed here.
Maintenance-free for 15 years
- Rendering plant (new facility)
- This facility had been using surface aerators, but these suffered from several issues: the release of foul odors and the spraying of liquid out into the facility surroundings, as well as difficult, burdensome maintenance. OHR AERATORs were introduced into the newly-installed additional aeration tanks.
- Installed OHR AERATORs: model AE-130 × 24 units per tank × 2 tanks = 48 units total
How to install
No need to drain the tank or anchor the aerator to the tank floor
Top